Polyurethane Foams: Versatile Materials with Multiple Applications
Density Considerations
This basic characteristic will determine how light or heavy the material will be. The advantage of low-density foams is that a small amount of starting material will fill a large space. Lightweight foams can be cost-effective. On the other hand, dense foams can be extremely strong and durable.
Flow and Speed of Cure
The reaction rate is controlled by a few variables. It is possible to design fast gelling into the reaction. This can quickly limit the flow of the liquid before it starts to set. Because a bit of flowing is sometimes helpful, it is also possible to slow the cure just enough to allow the liquid material to spread into all the spaces that need to be covered and filled.
Fire Retardants
Polyurethane Foams can be used to block air flow and seal spaces in buildings. In addition, it is possible to add fire retardants to limit the spread of smoke and fire. Polyurethanes designed with this feature will self-extinguish.
Closed Cell vs Open Cell
The bubbles in a foam are referred to as “cells”. A fully intact cell is called a closed cell, and an open cell is therefore one that has a connecting opening to another cell(s). The higher the closed-cell content, the more watertight and airtight the foam (typically preferred for sealants). In some cases, the preference is to open the cells to allow air and water to flow through the foam. This can also give the material some elasticity. It can also allow water to drain through it (e.g., a spongy dishwashing scrubber). For applications requiring airtight or watertight performance, a closed-cell foam is a must.
Packaging and Application of Polyurethane Foam
The components of the polyurethane foam must be well mixed to initiate the reaction. This can be done mechanically with a mixer. For products used on site, polyurethane foams are available in convenient packaging such as side-by-side “burst pouch” mixing bags. They can also be dispensed from cartridges through a static mixer. In this package, the two parts must be volumetrically balanced and should combine easily to ensure proper mixing. Developing this total package solution is done through the formulation as well as the mixer design. The viscosity of the unreacted components influences the ease of dispensing as well as how thoroughly the two mix through the static mixer.
Physical Testing of Polyurethane Foam
Polyurethane foams can be formulated to have excellent adhesion to different surfaces. They can be very strong and rigid or soft and flexible. Polyurethane can be tested for density, moisture absorption, compressive strength, and tensile strength.
Performance Testing of Polyurethane Foam
Testing specifically to the end use is key to ensuring proper performance. This can include hydrostatic testing, air flow testing, fire, and chemical resistance. It is also important to test compatibility with any components the foam remains in contact with, such as cable jackets.
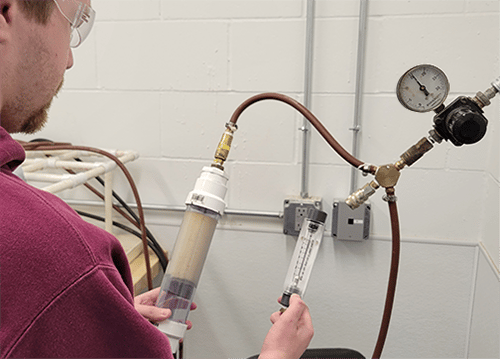
One-Part Foams: A Comparison
One-part aerosol “gap and crack” sealants are very common at DIY and hardware stores. These one-part foams are very different from the isocyanate/polyol two-part systems discussed above. One-part foams depend on aerosol propellant for virtually all of their expansion. Following this expansion, these foams depend on available environmental moisture to cure the resin and create strength. The overall strength of these one-part foams is often far inferior to that of isocyanate/polyol two-part foams. Some common characteristics include:
-
- Low-density, lightweight foam
- Limited cured depth of 3-4 inches (7 –9 cm)
- Long cure cycle
- Higher open-cell content
What Makes a Good Polyurethane Foam?
Because an infinite number of formulations is possible, polyurethane foams can be tailored to fit the purpose of very specific applications. Variations can address cure rate, flow dynamics, reaction temperature, component compatibility, final density, cell structure, fire retardancy, elasticity, tensile strength, and a host of other desired characteristics. One-part, open-cell foams available from DIY stores are designed as inexpensive options for the broadest possible range of end uses. However, this also tends to make them less than ideal for any single application. Why buy adequate when great is available? For sealing critical infrastructure, such as expensive electrical or communications cables in conduit, where robust, watertight protection is required, a “good foam” is better defined as a two-part, closed cell mixture designed and tested specifically for that environment. Any perceived savings from cheap, one-part, open-cell foams quickly vanishes when the cost of failed seals and the resulting damage is factored in the equation. Thus, it makes sense to seek out foam manufacturers capable of producing targeted formulations for optimal performance.